Packaging Machines Maintenance: 3 Questions to Ask Your New Supplier
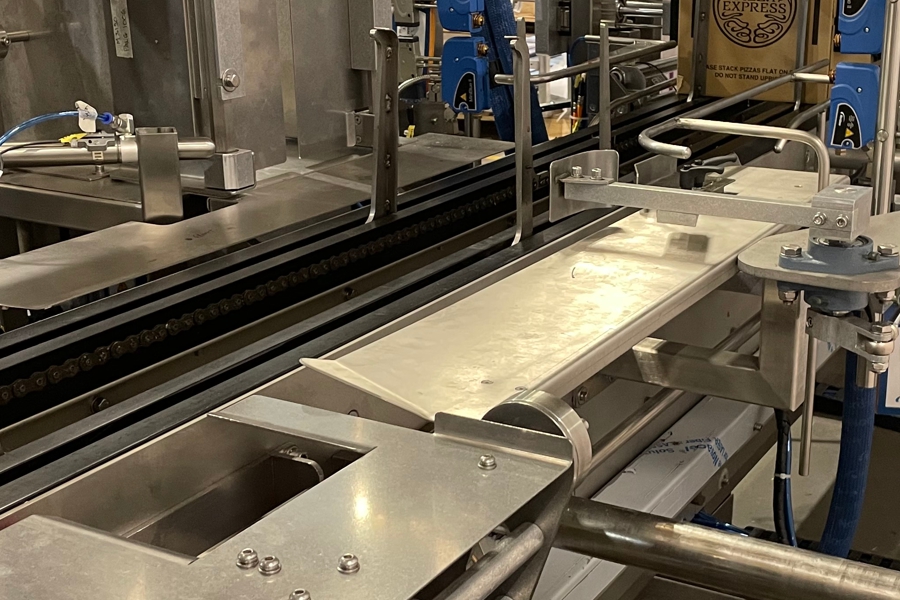
Assessing your packaging machines maintenance needs is an important part of implementation, whether you’re fully operational or just starting out with automation. As a global supplier, Jacob White knows how critical it is to get service and maintenance just right. We’ve put together three of the top questions to ask your new packaging machine supplier.
Do you provide operator training and technical support?
This may seem like an obvious question, but it is one of the most important to ask and should never be assumed. Training packaging machine operators in set up, calibration and testing of machinery forms a basic part of the overall maintenance strategy.
Talk to your new packaging machine supplier about operator training and find out more about the complexities of the machinery. This may help you to make important decisions about the type of packaging machine you decide to implement, particularly if your staff turnover is high or seasonal. It is worth remembering that some fully automatic packaging machines generally require less intervention.
It is also a good idea to discuss the supplier’s availability in terms of remote technical support. Often, most operational issues can be diagnosed and handled during a phone or video call.
Can you help us to plan a regular maintenance program?
Regular maintenance planning can help to ensure that machinery runs as seamlessly as possible with minimum downtime. While some of the best modern packaging machinery requires little maintenance and cleaning, knowing what to look for in regular checks and tests can also potentially flag a small issue before it grows into a bigger problem.
Your supplier can help you to plan regular maintenance and checklists and provide a spare parts list that may contain high, low and medium wear parts. This could include parts that are more likely to need a replacement or those which may carry a long delivery lead time, for instance.
What happens if I need a local maintenance team?
Regardless of regular maintenance and careful operation, there may come a time when the only solution to an issue is an on-the-ground technician. If this is the case, or there is an emergency breakdown situation, it will be critical to minimise downtime.
Ask your new packaging machine supplier to outline their procedure for an in-person maintenance visit. Do they have a local option? If your supplier is located abroad, this will be an extremely important question to ask and flesh out.
The cost of packaging machines maintenance
Basic training in operation and maintenance is often typically included as a part of the sales and installation/handover of the new packaging machine. It is a good idea to confirm any maintenance contracts and associated costs for regular servicing, emergency call outs and additional training sessions if required.
Your supplier should be contactable for assistance with parts orders and able to provide their average timescales. These are important elements to discuss during the consultation stages and can help you to make the right decisions about the systems and machines that you implement.
Packaging machines maintenance and service at Jacob White
As global suppliers of packaging machines, we make sure that our customers can access assistance for all their sales, installation, spares and service queries whenever they need it.
We have offices around the world in addition to highly skilled, trusted agencies that deliver vital backup, reassuring our clients of our dedicated attention, when they need it most. Talk to us about your packaging needs and find out more about parts and service here.